PROJECT HITLESS
A smart shoe that aims to assist a process we take for granted: walking.
Robotics/Product Design
Arduino, ultraviolet sensor, vibrating motor, wood
It's the 21st century. How do we still let ourselves run into things when walking? Three students decided to answer this question by providing a solution: footwear that warns you before you stumble.
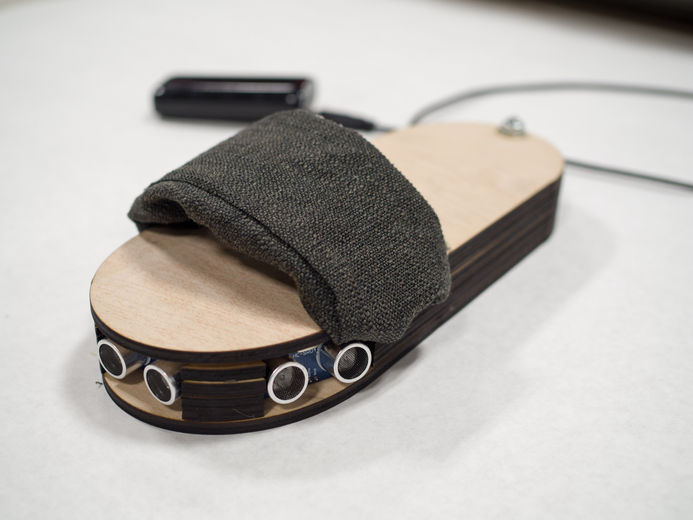
Process:
When creating such a product, we started off by trying to really understand the user. Through conducting user interviews and talking to a large number of people, we were able to draft user personas.


After we had user identities, we were able to craft user scenarios in which a product like ours would be useful. Doing this was helpful for us to convey our idea and its usage to people. It also helped us consider real-life implications of the product. Additionally, both the personas and scenario were stepping stones in understanding the most user-friendly design based on principles such as usability, accessibility, memorability and visual appearance.
From here, we were able to make decisions such as the number of sensors and motors and their placement for the purposes of prototyping our product. We ran through a series of sketches, low-fidelity prototypes and iterations until we reached our final version. We used different prototyping materials and ended up using an Arduino, laser-cutting wood and fabric for the final. We were also inspired by an ancient Chinese shoe-making technique. This technique allowed us to split our components into different sections which would maximize comfort for the user. With the Arduino at the bottom-most level and the vibrating motors at the top-most, we were able to account for cushioning for the foot while still being able to feel the vibrations. These process photographs document the journey that our design underwent:
Reflections:
Our prototype generally had several flaws such as wood as the choice of material and range of sensors. A lot more user testing was required in order to figure out the optimum range so that a user would get notified at the right moments, rather than being alerted either too often or not enough. A lot more research was also required into the ergonomics of shoes and general footwear design processes as well. A future iteration would also account for the battery by having an in-build rechargeable power source instead of a battery pack sticking out of the shoe with a wire. Despite its evident flaws, this prototype was quite successful in areas such as its layered structuring, placement of motors and sensors and delivery of message. Ultimately, there is a lot further this design can go, yet there is a lot that it teaches us with the way it is now.